Drop-on-demand inkjet printing
After the production of the first inkjet printers more than 50 years ago, inkjet technology has evolved into many more applications. It is used for coating generation, laying down thin electrical tracers on PCBs and in the display market for creating OLEDs, to name a few. When simulating a single inkjet droplet shot out of a nozzle it has to be ensured all relevant physics are accounted for. Such simulations can save a lot of time during development or in error analysis, because the impact of the governing parameters (like the applied pressure pulse, nozzle shape or ink surface tension) is easily isolated and tested.
Modelling surface tension driven flows
A pressure pulse is applied at the back end of the channel, mimicking the shock-wave created by a piezo-electric or thermal element. The pressure pulse travels through the ink and is amplyfied in the nozzle, after which a droplet shoots out. The droplet stays connected to the ink inside the resevoir, untill its surface tension is overcome and the droplet breaks free. The performance is often dependent on the droplet properties, like the speed, shape, volume and size and number of the satellite droplets, which can all be deducted from a CFD simulation as in this example.
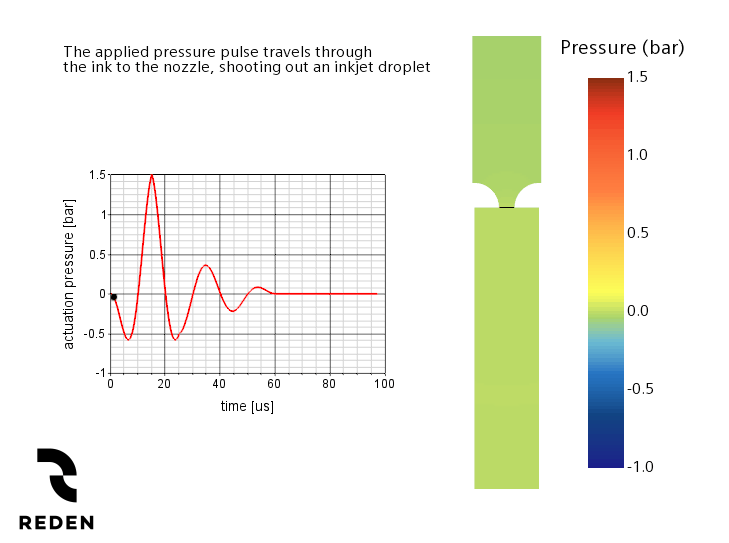
Building confidence: comparing with known results
Below, the simulated droplet is validated for its shape at eight timestamps: 10, 20, 30, …, 80 µs. The left figures are photo’s from experiments [Wijshoff, H. (2008). Structure- and fluid-dynamics in piezo inkjet printheads], the right are screenshots from the CFD simulation performed at Reden. Similar nozzle size and pressure pulse is applied.
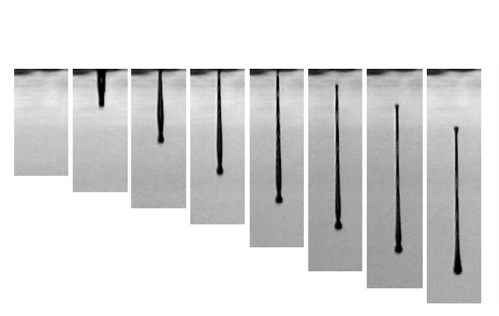
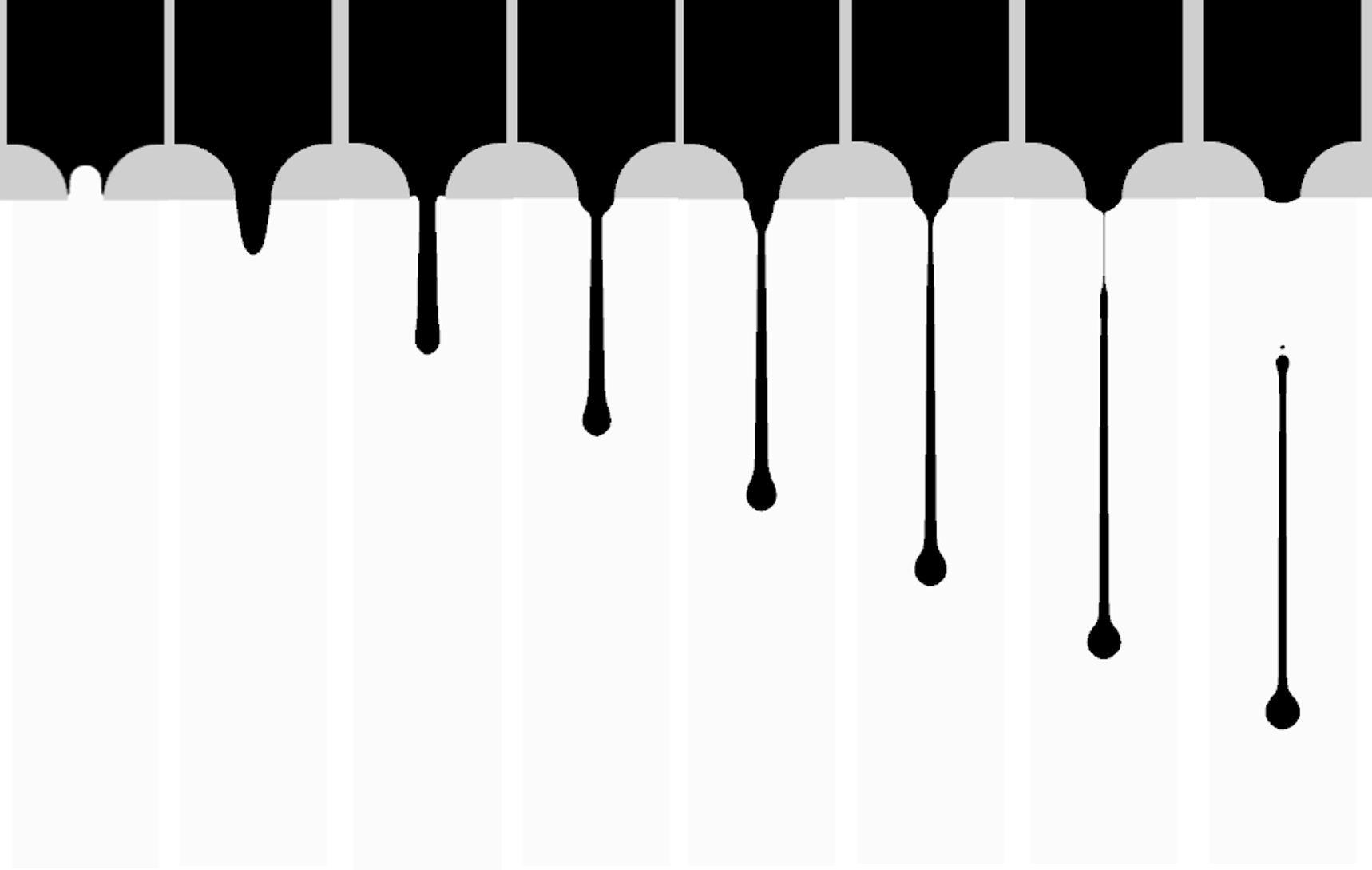