A small heap of iron powder on a table, who would think this was a possible energy carrier? It is certainly easier to transport, and probably safer than hydrogen; the lightweight gas that is infamous for its explosive nature, and that has to be compressed to a very high pressure to have a useable energy density. Iron can supply energy, because, just like hydrogen, it can be used as a fuel. You could get the same amount of energy from a one litre carton full of iron powder as from a 12.5 litre tank of H2 at 350 bar pressure! (or 0.7 litre of petrol). The tank containing the hydrogen is probably heavier than the iron powder [1].
We at Reden like to see the relevant numbers, to get a feeling for a new technology. But first, how can iron serve as an energy carrier?
Iron and hydrogen have in common that they are available in large quantities in oxidized form (iron ore and water). To ‘de-oxidize’ iron requires a lot of energy, which is released in the form of heat when iron (or steel) is allowed to rust. Usually, rusting occurs slowly, so that the heat is lost without being noticed. If iron can be made to rust (i.e. oxidize) quickly, very high temperatures can be reached.
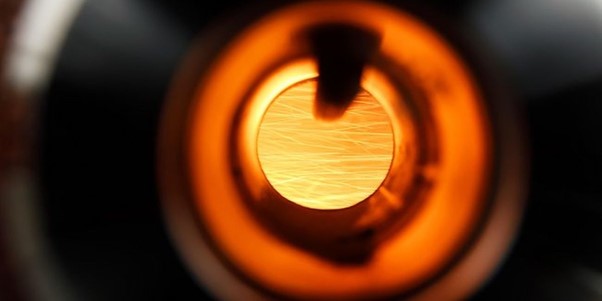
As a consequence, iron in the metallic, unrusted state can be seen as an energy carrier. To obtain it from iron ore, energy has to be supplied, in order to ‘un-rust’ the iron ore. This releases the oxygen. If the iron is later re-united with the oxygen by rusting/burning/oxidizing (chemically the same), the energy is released. This cycle can be used in several ways to store energy.
Method 1: iron-air battery
The first is the iron-air battes being developed by Form Energy. The low price of iron (certainly compared tolithium, the key component of Li-ion batteries) is a big advantage; iron isavailable in large quantities.
Method 2: fuel
The second way to store energy in iron is to use it directly as a fuel. The start-up company Rift (Renewable Iron Fuel Technology) is developing the idea of burning iron powder to supply heat without CO2 emissions. In a newspaper article, this is presented as ‘an alternative energy source’ [3]. A pilot installation is in operation at a beer brewery [4].
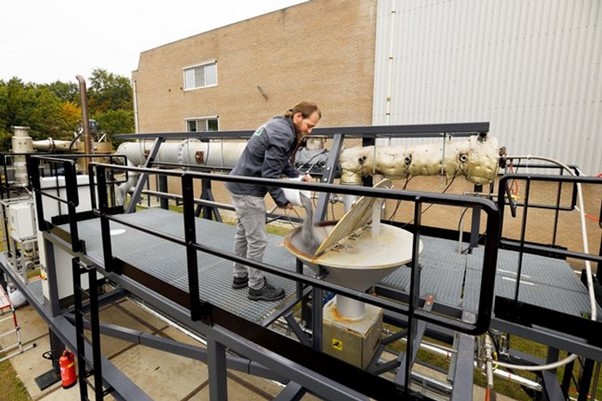
In contrast to common fuels, the combustion product is solid iron oxide: rust. For fast combustion and easy handling, iron powder is used, and the product is powder too, which is easy to collect and transport.
The regeneration is done using hydrogen, which is less noble than iron, and therefore manages to ‘steal’ the oxygen from the iron. The product is now new iron powder, which can be separated and transported easily.
[1] FAQ Guide - Hydrogen Tank (types, characteristics, design) | HYFINDR.COM. A tank for 4 to 6 kg of hydrogen with a mass of 100 kg is mentioned; 12.5 litre at 350 bar is roughly 0.36 kg of hydrogen.
[2] ‘Rusty’ batteries could hold key to Minnesota's carbon-free power future | MPR News.
[3] Trouw, 21 February 2023.
[4] RIFT | Igniting the clean fuelrevolution (ironfueltechnology.com).
Working the numbers
Let’s try to assess the energy content of a kg of iron powder, and the efficiency of the system. A simple overall cycle is shown in the figure below. I do not know if the combustion of the iron powder does proceed all the way to Fe2O3, but this would be the ‘best case’, so we consider it here. According to Wikipedia, the standard enthalpy of formation of this oxide is: 824.2 kJ/mol, which means that burning 1 kg of Fe-powder yields 7.39 MJ of heat. Iron powder has a relatively high energy density, for comparison: coal: 24 MJ/kg, petrol 47 MJ/kg, Li-ion battery 0.360–0.954 MJ/kg.
The (re-)generation is done using hydrogen, which is the product of electrolysis (if it is green). This costs 180 MJ/kg of H2 [5] (the thermodynamic minimum is 143 MJ/kg). When using hydrogen as an automotive fuel, another 54 MJ is needed for compression!
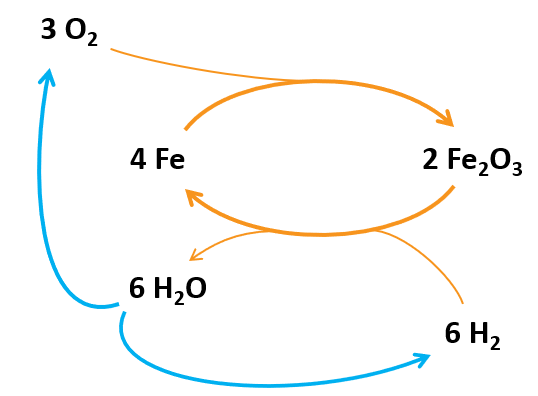
The energy balance of the cycle is (for 1 kg of Fe):
- Combustion of Fe: 7.39 MJ is released
- Production of H2: 9.75 MJ in practice, when excluding compression. Theoretically this is 7.74 MJ, which implies an efficiency of (7.74/9.75=) 79 %.
- Regeneration of Fe2O3: 7.74 – 7.39 = 0.36 MJ is released.
The great advantage of this cycle is that the powders can be transported easily: in bulk, and without the need for pressurised tanks or temperature control.
The efficiency is limited by the efficiency of the electrolytic production of hydrogen. The energy output (heat) of the combustion is 76% of the energy needed (electric) for the production of the hydrogen. If the heat generated during regeneration is added, the efficiency is 76 % + 3 % = 79 %. In that case, the iron cycle is free of losses (except for transport).
It is interesting to compare this efficiency with that of a ‘hydrogen only’ cycle. We consider two cases:
- Industrial use for heating.
- Transportation.
Case 1: hydrogen as an industrial heating fuel
For industrial use, high pressure compression is not necessary if large enough pipelines are present between the plant producing the hydrogen and the oven or boiler using it. Most processes require heat at a much higher temperature than the boiling point of water. However, no less than 15% of the heat of combustion of hydrogen is only released as the water vapour condenses, at 100 ⁰C. If no low temperature uses are at hand, the efficiency of the cycle drops to (100% - 15%)*79% = 67 %
Case 2: hydrogen as a transportation fuel
For transportation use, hydrogen needs to be compressed, reducing the efficiency to the point of use (electricity to hydrogen, compressed) to 143/(180 + 54) = 60.9%. It is technically possible to recover some of the compression energy, but in practice, most of it is lost.
It is further interesting how the hydrogen is used in the vehicle. According to Wikipedia, the efficiency of fuel cells (electric energy out/chemical energy in) is between 40 and 60% (say, 50%). The overall efficiency of a vehicle with a fuel cell on hydrogen, could therefore, be 30.5% (50% of 60.9%).
If hydrogen is used in an internal combustion engine, which has a thermal efficiency of 22% [6], the overall efficiency becomes 60.9%* 22% = 13.4%. If, for comparison, the iron powder is used in a car to fuel a heat or steam engine, the conversion efficiency is probably 25%, so the overall efficiency becomes 79% * 25% = 19.8%.
For a detailed analysis, more detail of the installations and equipment must be known, but a first order analysis shows that iron powder as a cyclic carrier of (green) energy is more efficient than using hydrogen for industrial process heating (79% vs. 67%). For transportation fuel, hydrogen is more efficient if the car uses fuel cells (30% vs. 20%), but if hydrogen is used in an internal combustion engine, it is less efficient than iron powder.
There are other features which speak in favour of iron powder. It is available in large quantities, can be stored and transported safely and cheaply, and can be stored indefinitely, unless you allow it to rust!
[5] Electrolysis of water - Wikipedia.
Conclusion
Iron powder is a promising candidate for the energy carrier for industrial processes requiring heat. It could even be used in a heat engine or steam cycle to deliver mechanical work.
The main advantages of iron powder as an energy carrier are:
- Iron is available in large quantities.
- It burns without producing CO2.
- The combustion product is easily captured (solid powder with high density).
- The rust powder can be re-generated using hydrogen (green, please!)
- Both iron powder and rust powder can be transported easily, without danger.
- The energy is released at a high temperature, so that it can serve to power industrial processes.