Treating skin cancer
Too much unprotected sun exposure can lead to skin cancer. Exposed parts of the human skin, such as the head, arms or legs, can develop life-threatening melanoma. Photodynamic therapy is a promising treatment for skin cancer. A drug activated by light can disrupt the cell division mechanism of cancer cells, causing them to destroy themselves. This therapy has a history of using either sunlight or high-intensity artificial light. To create controlled, safe conditions for therapy, homogeneous, low-intensity illumination of the skin is required. This can be provided by a fabric with optical fibres that are fed with laser light. Serving as an application example is a kind of bathing cap made up of light-emitting fibres that is pulled over the head of a scalp cancer patient. Such a flexible light source can be made by weaving or knitting.
Modelling the weaving process
Research into light-emitting fabrics has been performed in the European Photonics21 project Phos-Istos, with clinical research partners, weaving and knitting specialists, and laser and fibre-optic suppliers. Reden got involved because project partners had been impressed by our earlier simulations of the weaving process, which had long been considered an intricate challenge by the simulation community. For multilayer woven fabrics of composite materials, we had fathomed the virtual world of warp and weft. We had modelled the dynamics of weaving and used finite-element models to calculate the stresses and strains and the curvature of the various fibres used in the process.
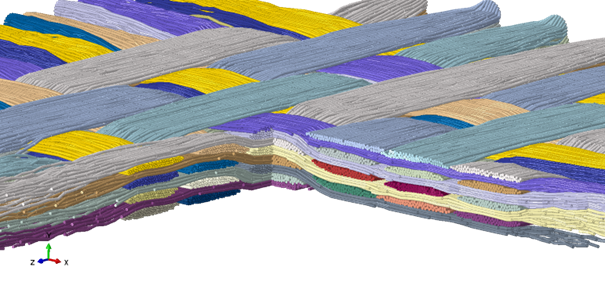
In these previous weaving studies, we performed detailed calculations on a “unit cell” of the weave pattern, created with multi-fibre yarns, after which this unit cell was reproduced several times to create a model of a complete fabric. We used this model to investigate the effect of process parameters such as weave type, fibre properties and yarn pretension to predict the mechanical properties of the resulting fabric at the meso and macro level, to determine the local structure of the fabric at corners, edges and holes, etc. For the notoriously “difficult” case of fabric pre-forms for composite product applications, we found excellent agreement between the model simulations and experimental results, with differences for all relevant mechanical properties below 8%.
In the Phos-Istos project, optical fibres were the natural choice for achieving light emission. Because of the flexibility required for weaving and knitting, the polymer version was used. Below a plain weave simulation with monofilament fill yarns (optical fibres, in white) and multifilament warpyarns (in red) is shown.
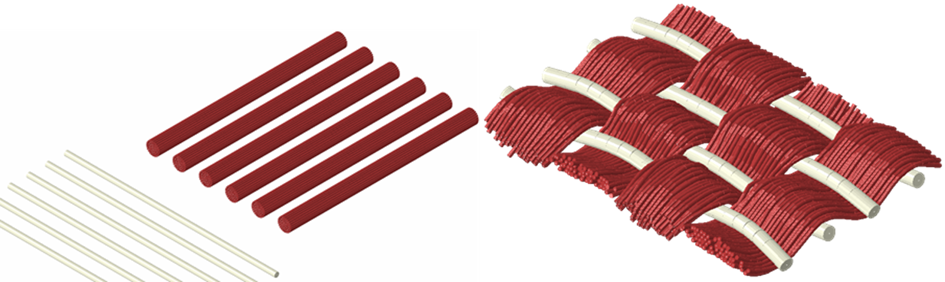
Optical fibres, made up of a core and a cladding, can be fed with laser light. When the fibres are bent, some of the propagating light is emitted due to refraction occurring at the core-cladding and cladding-air interfaces. The light emitted at any point depends on the local curvature of the fibre and the intensity of the light that has remained inside the fibre after refraction in the preceding ray trajectory. To create a more or less homogeneous light output profile over the length of the fibre, laser light is fed from both ends.
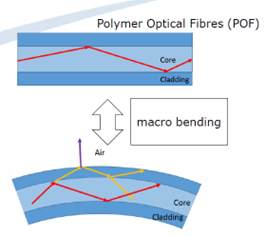
Performing design of experiments
To study a light-emitting fabric, we performed extensive finite-element simulations of the weaving process. With ray-tracing simulations, we determined the light output performance of individual fibres and the integrated output of a complete fabric. For this, we successfully created our own code, as commercial ray-tracing software did not support the optical modelling of fibres in combination with mechanical finite-element modelling. Results were in agreement with first-principles considerations. For example, higher warp yarn tension yielded a higher fill yarn curvature, resulting in a higher light output. Interestingly, we found that light emission not only occurs at the point of curvature but also in the wake of that point.
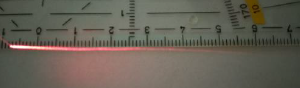
We automated the weaving simulations to perform a full design of experiments (DoE), using a total of 13 different weaving patterns with each time three values for the yarn pretension. In particular, we looked at the efficiency of the various patterns and their homogeneity over the complete surface of the fabric. Our simulations predicted the satin 8 weave pattern to have the best homogeneity in light output, as was confirmed by experiment. We included the DoE results in our Reves DSE tool to support design-space exploration in future weaving model studies.
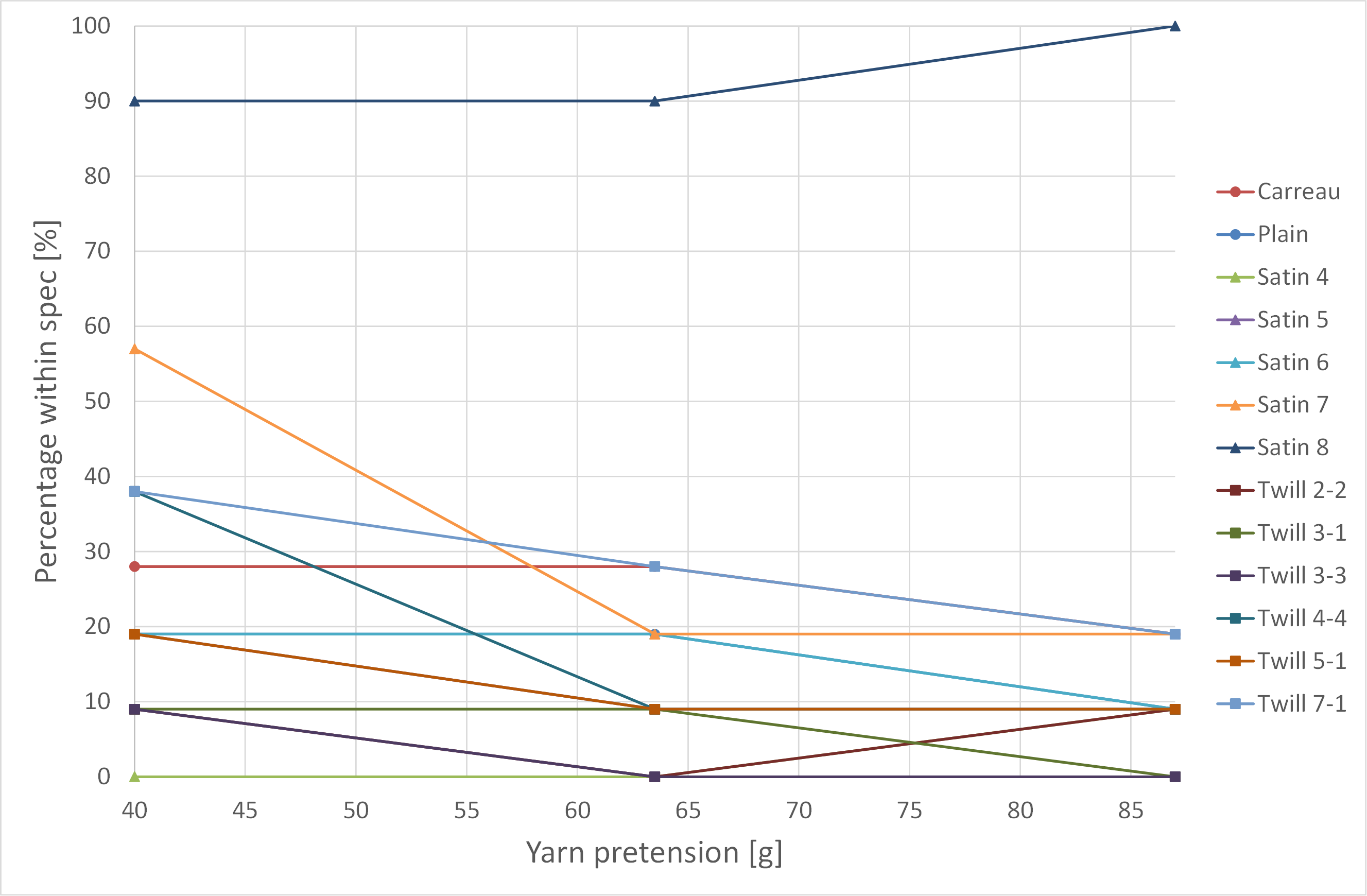
Making weaving and knitting predictable
In the same vein, we extended our weaving simulation expertise to the domain of knitting, in order to investigate the knitting of a light-emitting cap. Producing smoothly alternating curved fibres that resemble sine waves, knitting was found to show a much higher experimental reproducibility than weaving, which posed quite a challenge to physically control the yarn pretension. We set up a model of the knitting process and performed ray-tracing simulations. A result of these simulations is shown in the image below, where the light intensity in the fibrecore is shown: high intensity (red) at the entry side and low intensity (blue) at the exit side of each fibre. The simulation results yielded a good match with experimental results.
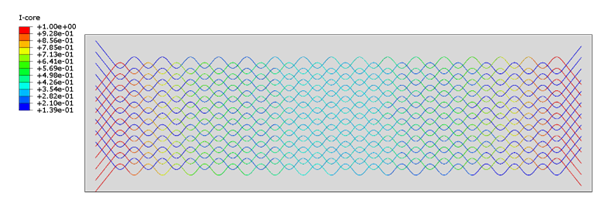
The encouraging results gave us confidence that simulations can help speed up the development of new weaving projects. This is because they reduce trial & error, thus saving on the time-consuming set-up of the weaving loom in the exploratory phase, with up to 5,000 warp threads for each new design. In this way, we succeeded in making weaving and knitting processes more predictable, not only from a mechanical perspective but also in terms of optical properties in case of light-emitting fabrics. All in all, we were able to shed more light on fabric manufacturing.
