Contamination control
Semiconductor R&D continuously focuses on keeping up with Moore’s law – the observation that the number of transistors on a chip is doubled roughly every two years. As a result, state-of-the-art chip manufacturing technology can accommodate the exponential increase in demand for more processing power and memory capacity to enable new developments in AI, Big Data, mobile/5G communication and other aspects of the ongoing digitalization.
To increase the number of transistors per chip, by decreasing their size, extreme UV lithography has been developed. EUV radiation, due to its short wavelength, can produce smaller features and hence enable smaller transistors. One of the big challenges is contamination control. The process works under vacuum to prevent the absorption of EUV radiation and the subsequent decrease in output. Measures to ensure cleanliness include suppressing contamination sources, cleaning surfaces and applying shielding gases to divert contamination from the critical regions. For over ten years, Reden has supported R&D projects in this area with advanced model simulation studies.
IC technology for the 2nm node
One of the latest examples is the EU-funded IT2 project (IC Technology for the 2nm Node), coordinated by lithography world market leader ASML. The overall objective was to extend the scaled semiconductor technology roadmap to the next node in accordance with Moore’s law. IT2 focused on next-generation extreme UV lithography, in particular technology options for equipment, processes and metrology required for realizing 2nm CMOS logic technology. To gain insight in the dynamics of particle contamination and derive guidelines for the design of low-contamination systems, the IT2 project included the development of simulation strategies for the contamination process, for which Reden was involved.
Modelling strategy
However, simulating the movement of molecules and particles in a low-pressure vacuum environment is not straightforward. It requires a two-step approach, first computing a flow field, followed by inserting particles from a contamination source in this flow field and determining where they end up. If that is in a critical spot that should be protected from contamination, then preventive measures have to be taken, preferably already in the design phase.
To reduce the computational effort, a multi-scale approach was followed for flow modelling. The basis is a 1D network model that can be locally refined – for example, in regions that have to stay clean – using detailed flow simulations, such as CFD (Computational Fluid Dynamics). The resulting multi-scale flow field can be used for contamination prediction, particularly for the critical regions, while still taking into account the influence of other areas. Maintaining the network model with integrated local refinement, instead of performing uncoupled simulations, has several advantages: better boundary conditions, understandable and usable models, computational efficiency, and better flow predictions.
Connecting flow regimes
Next, the question was which methods (solvers) to use for the detailed flow simulations and how to interface between them. Obviously, in a low-pressure, rarified gas flow, CFD simulations are only valid if there still is some kind of continuum. In fact, four different regimes can be distinguished, characterized by the Knudsen number, a measure of the mean free path of a particle in a medium. The extremes are the hydrodynamic/continuum regime and the free molecular regime. Starting from the continuum regime, with pressure decreasing and hence Knudsen number increasing, eventually near a wall the continuum flow condition of zero particle velocity will no longer hold. Particle velocity will be non-zero; this is called slip. When pressure even further decreases, a real transition regime toward free molecular sets in.

The free molecular regime can be described by the Boltzmann equations and can be solved by DSMC (Direct Simulation Monte Carlo) tools of statistical mechanics, which are computationally very demanding and can therefore only be applied to a limited number of particles. On the other hand, the hydrodynamic regime can be described by the Navier-Stokes equations of continuum mechanics; CFD is used to obtain approximate solutions. For the intermediate regimes, we developed a hybrid solver that couples the DSMC method with the CFD simulations, to restrict DSMC model size while ensuring correct boundary conditions. In the near-continuum slip regime, the validity of CFD can be maintained by introducing a ‘fiddle factor’; this represents a change in boundary conditions to capture rarefaction effects along walls.
Particle tracing
Having settled the issue of flow simulation, we turned to particle tracing. Commercially available software did not include features we required, such as non-spherical particles and sophisticated wall bouncing models, nor other potential forces acting on the particle (such as thermophoresis, electrostatics or magnetism). Therefore, we developed proprietary Python code for predicting trajectories by tracing – forward in time – the positions and velocities of particles, while incorporating interactions with the boundary and the flow field. Because of the small number of particles and their small size, particle-particle interaction was not included. Still, these forward particle tracing (FPT) simulations are very inefficient, as only a small part of the released particles reach the target area, i.e. the contamination-critical region of interest.
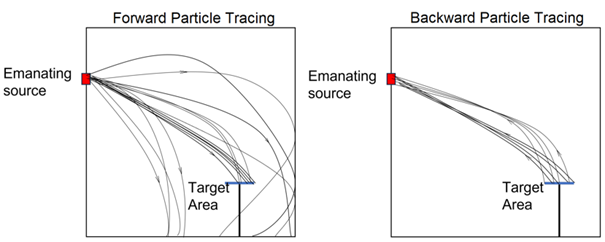
As an alternative, we developed an algorithm for backward particle tracing (BPT). With this method, particles that have reached the ‘target’ can be traced back in time. Now, only relevant trajectories are calculated, which is of course very efficient. This comes at a cost, however, as in these inverse simulations uniqueness is lost: particles could have arrived coming from different directions and with different velocities. This prevents a perfect reproduction of corresponding forward-traced trajectories. We devised a method to deal with this, combining the advantages of FPT (accuracy and uniqueness) and BPT(efficiency and relevance).
Mitigating contamination problems
We made extensive study of the variables and other factors affecting the accuracy of our flow modelling results, which are prerequisites for the particle tracing analyses. This enabled us to optimize our modelling approach, leading to a viable solution path. Finally, we validated our FPT and BPT models with experimental and numerical data from literature. In this way, we have provided designers of semiconductor and other high-tech equipment with a reliable model that can help them mitigate contamination problems.
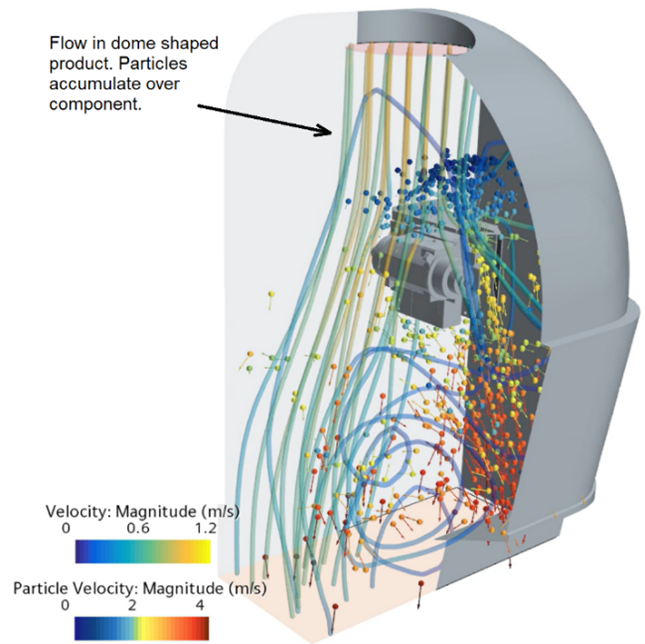
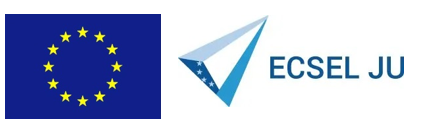